22.03.2025
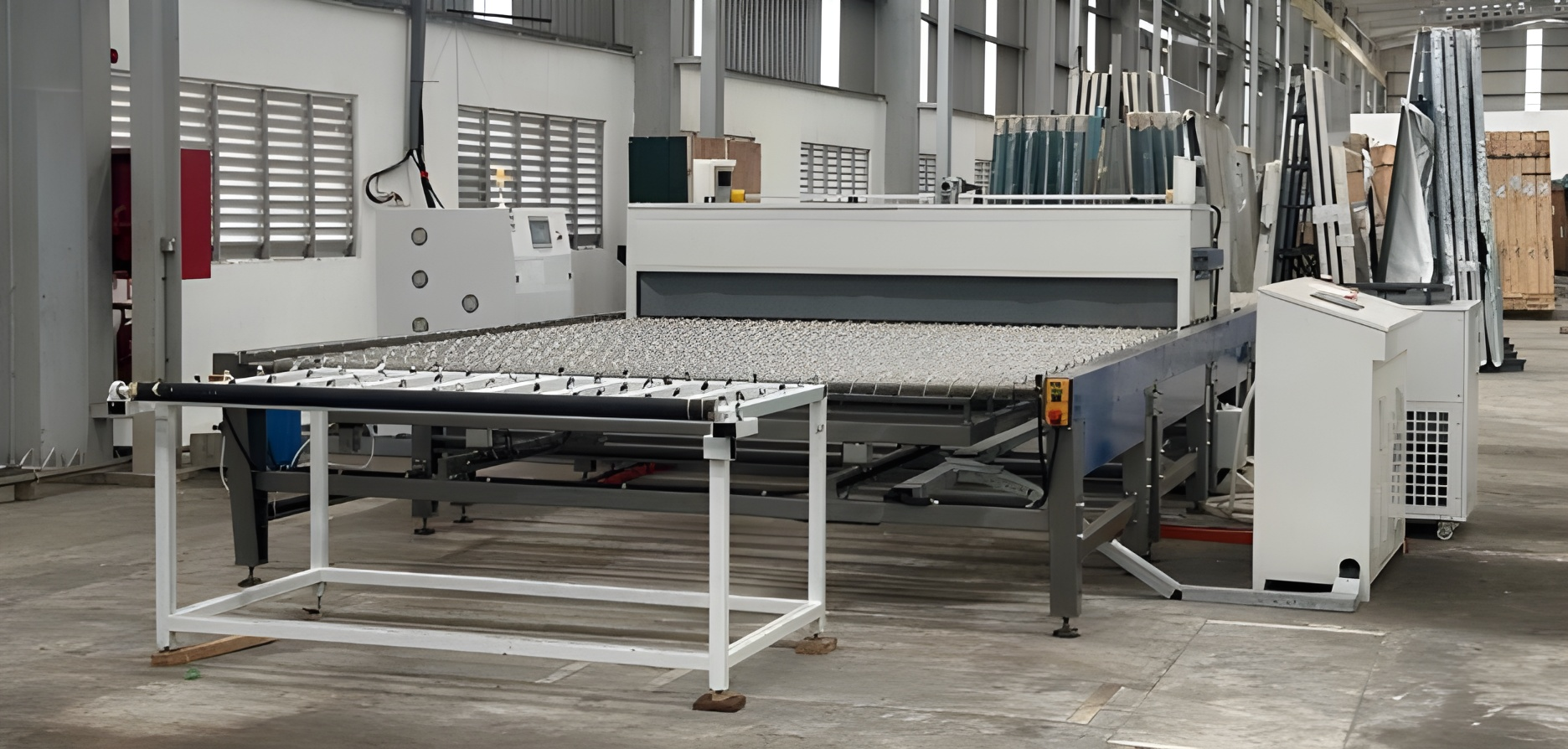
Crystal Group Unveils Groundbreaking Laminated Glass Technology
Crystal Group is proud to announce the installation and commissioning of Malaysia’s first UV-Cure Vacuum Lamination Line. This cutting-edge system, designed to support advanced safety interlayers, represents a significant advancement in laminated glass manufacturing in Southeast Asia.
Two-Step Production Process
The new system simplifies production into two stages, replacing traditional autoclave processing:
- Vacuum Heating
Uniformly melts the interlayer under vacuum conditions to ensure superior clarity and adhesion, even with decorative or shaped inserts. - UV LED Curing
Cures the laminated unit in minutes, producing strong, durable bonds with zero delamination risk.
Manufacturing Process of Normal Lami vs. NSI
Process Step | Normal Lami Process | NSI Process |
---|---|---|
Interlayer Type | PVB, EVA, SGP | NSI |
Equipment Used | Autoclave, Heating Chambers, Pressing Machines | Vacuum Machine, UV LED Curing Machine |
Temperature & Pressure | High temperature (130°C–150°C) and high pressure | Low temperature and low pressure |
Time to Process | Several hours, depending on thickness and size | Approximately 15 minutes per sheet |
Production Stages | Heating, Pressing, Autoclaving | Vacuum + UV LED Curing |
Delamination Risk | Risk of delamination, requires precise control | Zero delamination risk |
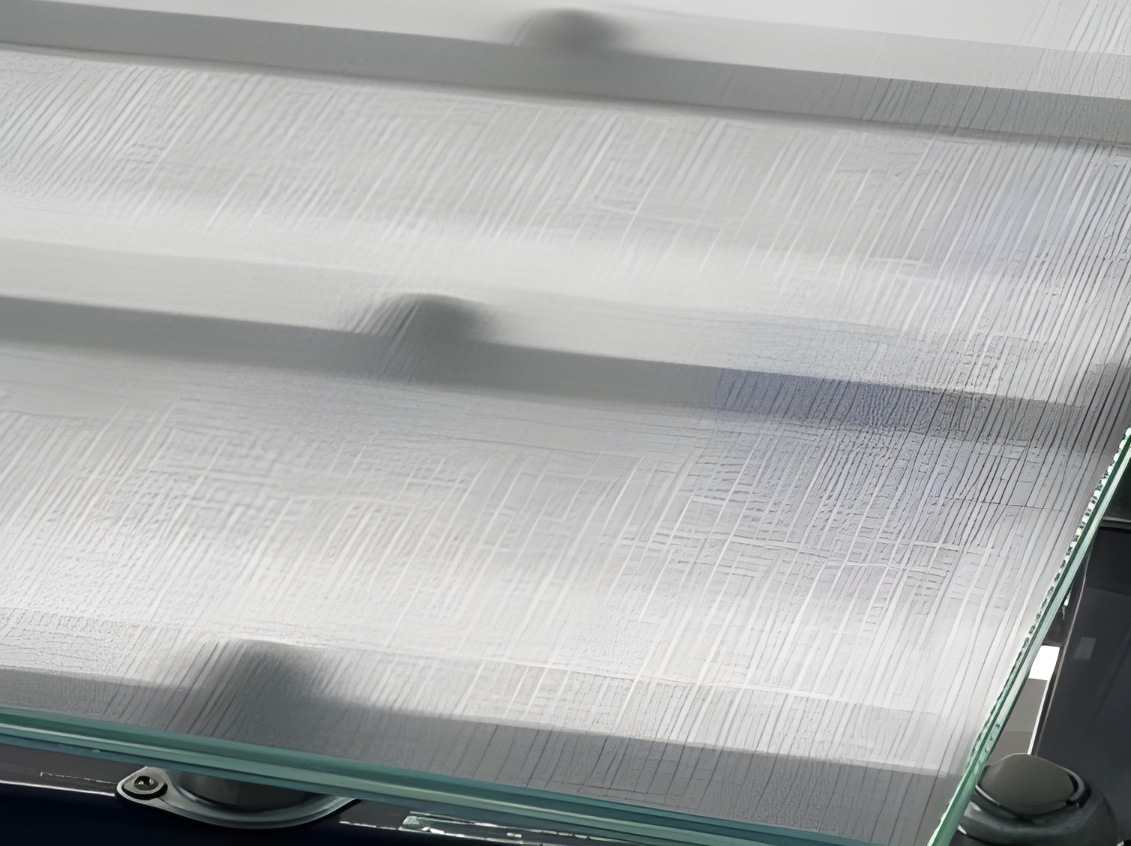
A Milestone for Malaysia
As the first company in Malaysia to install this UV-Cure Vacuum Lamination Line, Crystal Group sets a new benchmark for laminated glass manufacturing, offering unparalleled flexibility and performance.
For more information or inquiries, please visit https://crystalsafetyglass.com.my/nsi/.